Governed by the International Standards Organization, ISO 9000 consists of internationally recognized standards that relate to quality systems that are used to ensure that customers receive what they expect. In this way, it provides clear standards and guidelines on how to implement and improve your Quality Management System.
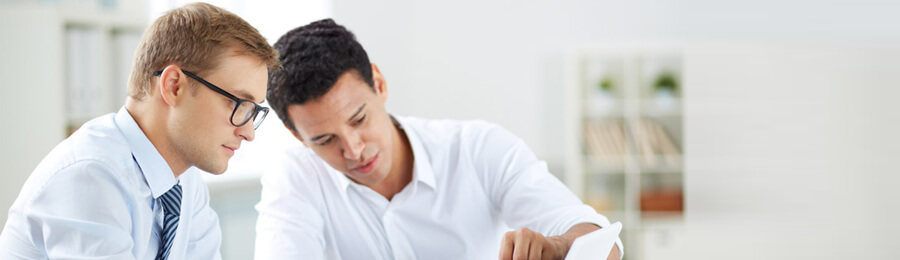
The standards within this family comprise the following:-
- ISO 9000:2015 – defines the details of quality management systems, which form the basis of the ISO 9000 family, while also specifying the terminologies used in these standards.
- ISO 9001:2015 – as the requirement standard, the primary goal is to direct organizations in attaining quality requirements, achieving appropriate regulatory requirements, improving customer satisfaction and obtaining a system for constant improvements in order to meet objectives.
- ISO 9004:2009 – offers guidelines for performance improvement according to the eight quality management principles. This standard outlines the principles used by senior management to improve organizational performance by allowing for the needs of all stakeholders, not only customers.
Key Content of ISO 9001
ISO 9001:2015 is constructed around 7 quality management principles:-
- Customer focus.
- Leadership
- Engagement of people
- Process approach
- Improvement
- Evidence-based decision making
- Relationship management
It was introduced on September 15th, 2015 and organizations have until September 28th, 2018 to implement the new standards. The main changes from the ISO 9001:2008 standard are as follows:-
- Ten clauses instead of Eight – The first three clauses in ISO 9001:2015 are largely the same as those in ISO 9001:2008, but there are many differences between ISO 9001:2008 and ISO 9001:2015 from the fourth clause onwards. The last seven clauses are now arranged according to the PDCA cycle (Plan, Do, Check, Act).
- A high level structure (HLS) – ISO 9001:2015 now has the same explicit structure as all standardized management systems, known as a ‘High Level Structure’ (HLS). This means that the core elements of ISO 9001, ISO 14001, ISO 22000, OHSAS 18001, etc. are the same from now on. Therefore, integrating various management systems will be simpler as the parts that cover the same topic are easily found in the standards.
- More focus on Input and Output – There is a greater importance on measuring and properly assessing the input and output of processes. According to ISO 9001:2015, you must closely monitor the inputs, such as raw materials, parts, labor, information and specifications, that are involved in the production process. You must also check that the output from the production process is of good quality.
- Risk-based thinking is crucial – Organizations are now strongly encouraged to use risk analysis as a means of identifying the challenges that they face. The addition of risk-based thinking has made the ‘preventive measures’ of ISO 9001:2008 redundant and these no longer appear in ISO 9001:2015.
- Context of the organization – The requirements and expectations of interested parties, the same as stakeholders, must now be anticipated in an organization’s products and services. You have to show that, as an organization, you understand and respond to the expectations of all parties concerned.
- Interested Parties – In ISO 9001:2008, customers were often named as being the only interested party. With ISO 9001:2015 this has been extended to also include all stakeholders such as suppliers, personnel, shareholders, legislative bodies, society, internal customers, etc. So an organization must be aware of the priorities and requirements of these interested parties’ and anticipate them in their products and services.
- Leadership and Commitment -The ‘management representative’ of ISO 9001:2008 is no longer mentioned and now quality is the responsibility of everyone at all levels in the organization.
- There is a desire to encourage the integration of the quality management system with an organization’s business processes and strategies. To accomplish that senior management and leadership must take responsibility for the effectiveness of the quality management system.
- Documented Information – Documented procedures or a quality manual are no longer a specific requirement. The term now used is ‘documented information’ and it concerns ‘information that the organization has to control and maintain’. So the information can be in any format and come from various sources and media not just paper.
Changes from ISO 9001:2000 to ISO 9001:2008
ISO 9001:2008 signified a minor upgrade and effectively provided explanations to the current requirements of ISO 9001:2000, along with changes designed to increase consistency with ISO 14001:2004. There were no new requirements.
Changes from ISO 9001:1994 to ISO 9001:2000
This was a major upgrade to the standard. Before the upgrade, the following three standards were incorporated:-
- ISO 9001:1994 – Manufacturing with Design & Development.
- ISO 9002:1994 – Production and Installation (No Design)
- ISO 9003:1994 – Final inspection and test
These were all amalgamated into a single standard, which is ISO 9001:2000.
For ISO 9001:2000 however, the 20-clause organization was removed and replaced with the 5 sections described above.
This standard is process-orientated, and tracks the operational principle of the Plan-Do-Check-Act (PDCA) methodology. The new standard progressed to a customer-oriented approach, requiring organizations to communicate with customers while also observing and reporting on customer satisfaction.
It also emphasized the need for improvements, and stipulates that an organization must assess the efficiency and appropriateness of its quality management system, while recognizing and implementing systemic improvements. Evidence of training was no longer adequate, and as an alternative, the efficiency of training has to be appraised.
As a final note, documentation requirements became less rigid and allowed better flexibility.